我公司10KV電動機VPI成型線圈採用少膠雲母帶。電動機的故障約有50%都要與絕緣直接或間接地發生關係。絕緣結構合理與否對電機的質量、有效材料—銅線、硅鋼片的利用率,直至電動機壽命及性能運行起到至關重要的作用。
一 電動機絕緣的構成:
電動機的整體絕緣由以下几部分構成:
導線本身自帶的絕緣;
繞組層間、相間絕緣;
繞組對地絕緣;
引線、連接線、端箍包紮的絕緣及繞組的浸漬漆。
這些絕緣分布在線圈或繞組的股間、匝間、排間、相間、對地處,以及導線(如連接線)、端箍的包紮上,它們與絕緣浸漬漆合在一起構成整臺電動機的絕緣。
二 每部分絕緣的構成、選用
1 股間絕緣
當電動機功率較大一點,仍選用單根導線,電密就要高。若加大導線截面積,則太粗的導線除使線圈加工、繞組嵌線帶來不便外,還有電氣上的弊病(如集膚效應)。因此採取用多根導線代替一根,達到降低電密的辦法。多根導線之間的絕緣稱為股間絕緣。它們用導線本身自帶的絕緣構成。
2 匝間絕緣
匝間絕緣的設置於匝間電壓、絕緣導線絕緣層的耐壓能力及浸漆工藝有關。
目前解決匝間絕緣的簡易辦法是在導線帶的自身絕緣上做文章,即選用絕緣層較為理想的絕緣導線。如聚酯漆包雙玻璃絲包線亞胺膜半疊包雙玻璃絲包導線均可直接用在10KV及以下、2000KW左右以下的無特殊要求的高、低壓電機的定、轉子繞組上,而無需另加匝間絕緣。若匝間電壓不太高,亦可用聚酯漆包單玻璃絲包線,雙邊絕緣層厚度僅為0.3mm左右。否則,宜選用亞胺膜疊包雙玻璃絲包線,雙邊絕緣層厚度為0.5mm左右。但無論選哪種,外層 有玻璃絲,它的作用:一是保護內層的漆膜或亞胺膜;二是在浸漆時能挂上較多的漆。若採用熱模壓工藝,多膠雲母帶在熱模壓過程中將擠壓出來的漆滲到這層玻璃絲上。以上兩種,特別是後者,幾年來在高壓電機上應用效果較好。
若設計者寧可導線絕緣層后點多占些槽部空間;製造或修理廠也舍得多花點錢購買絕緣層較好的導線;線圈加工、繞組嵌線及浸漆均做到“精心”,採用以上兩種導線,不必另加匝間絕緣,可以在很寬的範圍內基本上杜絕匝間故障。
若某些產品在使用中容易遭受瞬間高壓衝擊(如雷電),則在滿足檢驗結果的前提下,應考慮另加補強的匝間絕緣。
而在正常運行時,匝間承受的電壓=額定相電壓/每相串聯的匝數,僅能作為選用匝間絕緣時的參考數據,因為首匝承受的電壓有時要高於此值,特別是頻繁啟動及經常正、反轉的電機。
補強匝間絕緣的措施是:匝間加墊條(如亞胺薄膜,通常僅加在端部)、隔匝包或逐匝包。
目前隔匝或逐匝包一般採用0.14×25的三合一的粉雲母帶。若導線自身較好,半疊包即可。
不同匝間絕緣承受的電壓值
匝間絕緣結構 每匝承受的試驗電壓/V
聚酯漆包雙玻璃絲包扁線 400~500
雙玻璃絲包扁線0.1亞胺膜 >500~600
1000~15亞胺膜半疊包雙玻璃絲包扁線 >1000~1500
雙玻璃絲包扁線外層半疊包0.14×25三合一粉雲母帶1層 >1600~2400
聚酯漆包雙玻璃絲包扁線外層半疊包1層0.14×25三合一粉雲母帶 >2500~3000
3. 排間絕緣
對於電壓高、功率小、匝數多的電機,採用“雙排串”的線圈時。這是一個匝數為16的線圈。繞制時,第8匝與第9匝間的電壓就比較高,所以這兩排之間在認為需要的情況下(如電機在多雷地區使用;或者電機繞組導線的自帶的絕緣比較薄弱),就要加“排間絕緣”。因為第8匝和第9匝間的電壓較高,比如6KV的線圈,全線圈的試驗電壓為13000V,匝間電壓為13000V/16=812.5V, 第8匝的電壓是1~8匝的累計的電壓值,為812.5V×8=6500V,它與第9匝的匝間電壓再按812.5V考慮顯然不合適了。因此,應該在兩排之間加上排間絕緣。按照電機使用環境及導線自帶絕緣的承受能力,可以半疊包0.05mm的亞胺膜或三合一粉雲母帶,每排包或只包一排(有受壓程度而定)。
4.相間絕緣
對於成型繞組,靠線圈端部包紮的絕緣及線圈間的間隙即可承受相間電壓。如線圈間間隙比較均勻,線圈端部間墊塊的安放及線圈的綁紮處理的很妥善,對於雲母帶包紮的線圈,端部包紮的層數為槽部的2/3~1/2即可。比如,若槽部,極限圈的直線部分若半疊包12層,則端部半疊包6~8層即可。對於散嵌繞組,則要另加相間絕緣。其層數、材質與槽部相當即可。若槽部採用兩層,相間宜仍用一層(為嵌線工人容易操作)時,可按下列辦法處理。
1) 當槽部絕緣用一層0.2~0.5mm的NMN,加一層0.05~0.1mm的薄膜,若薄膜主要的用途是在槽口處“挽袖”,以加強槽口處絕緣時,相間只用一層0.2~0.25mm的NMN即可。
2) 當槽部用兩層0.2~0.25mmNMN時,相間可以用一層0.3mm的NMN.
相間絕緣的尺寸,要按繞組端部形狀裁剪。裁剪時,其外緣應大出每極相組線圈端部5mm左右;同時,還要與層間絕緣搭接10mm左右。
5.層間絕緣
當雙層繞組採用短節距時,在同一槽內異相的上、下層線圈間要承受電機的額定相電壓。因此,層間要加層間絕緣。對於成型繞組,若每個線圈均包主絕緣,則層間絕緣可以取消。但為了端部線圈間有間隙、嵌線時操作方便,以及填補同一機座號不同規格間線圈的高度差,也要加層間絕緣。通常F級絕緣電機用3240的環氧玻璃布板。其寬度尺寸=沖片槽寬-0.5 mm左右;長度~線圈伸出鐵芯的直線部分。對於散嵌繞組,則要選用與槽部絕緣相同規格的絕緣,但仍用1層為妥。其尺寸寬度要比槽的平均寬度大10mm左右,以保証上、下層線圈間被可靠地絕緣為度;長度應大於線圈伸出鐵芯的直線部分5mm左右。
6.對地絕緣
對地絕緣也稱“主絕緣”或“槽絕緣”,它是電機絕緣的核心。電機的質量、成本及溫升均與它有直接關係。因此按低壓、高壓;成型、散嵌;定子、轉子分述。
(1)低壓散嵌線定子繞組對地絕緣 就絕緣規範而言,1140V及以下均屬低壓範疇。目前低壓電機,無論是製造還是維修,95%以上均採用F級絕緣。僅在及個別產品,如軋鋼用的電機上,因環境溫度按60℃考慮,方採用H級絕緣。因H及絕緣電機用的軸承很難配套,所以儘量少用H及絕緣的電機。若非要用H級的,應在軸承處的通風散熱上採取措施,或將電機溫升控制在F級上。
低壓、散嵌線F級絕緣目前採用對地絕緣材料為:
0.2~0.25mmNMN(聚酯薄膜聚芳纖維紙復合箔);
0.2~0.35mmDMD(聚酯薄膜聚酯纖維紙復合箔);
0.05mm聚酰亞胺薄膜(6050)。
H級絕緣常用的材料為:
0.2~0.25mm NMN(聚酰亞胺膜聚芳纖維紙復合箔);
0.05mm聚酰亞胺薄膜(6050)。
F級、H級槽絕緣的尺寸、層數的規律相同,只是材質略有差異。
散嵌繞組的槽型一般均為梨形槽,為嵌線方便,槽絕緣放入槽內后應露出槽口,嵌線后將高出鐵芯部分剪掉,然後放入槽中,槽絕緣的長度,按機座號由小到大,每端應長出鐵芯5~20mm.
槽絕緣的層數:
小功率電機,1層0.2~0.25mmNMN;功率稍大一點時,在0.2~0.25mm NMN的內側加1層0.05mm亞胺薄膜。為補強槽口處絕緣強度,將亞胺膜在槽口處“挽袖”。
機座號大於280或1140V電機應選用2層0.2~0.25mm NMN,中間夾一層0.05mm的亞胺膜,共三層。亞胺膜仍“挽袖”。
槽絕緣的層數、厚度除與機座號、電壓有關外,還與鐵芯質量、槽絕緣材質的質量及導線本身自帶絕緣的絕緣強度以及繞組的浸漬漆有關。當後面這四項附加的制約因素都很理想時,槽絕緣就可以薄點,否則就要厚些。因此,槽絕緣的層數沒有明顯的界定範圍。股間、匝間、相同、層間、對地絕緣位置如圖3—4所示。
(2)低壓散嵌線轉子繞組對地絕緣,選用的規律同定子。稍有不同的是轉子電壓隨定、轉子繞組匝數比不同而在某一範圍內變化。轉子電壓與轉子電流的乘積,對於某一特定的規格基本上是一個變化很小的數值。若有的使用部門要求轉子電流要小,則轉子電壓勢必要高。此時,在選用槽絕緣上應予適當地考慮。
(3)低壓定子成型繞組對地絕緣
1)半開口槽分片嵌線繞組 為了提高cosφ,採用半開口槽。因此,要將一個線圈邊一分為二,即分成左、右兩半,稱為“分片式”線圈,兩個分片式線圈在端部將對應的各匝並聯在一起,構成線圈的上層邊及下層邊。
槽絕緣4可採用2層0.25mmNMN.槽絕緣厚度的取捨規律同散嵌線,即理想狀況下,可採用2層0.2mmNMN;否則,要採用2層0.25mmNMN,甚至2層中間還要加1層0.05mm的亞胺膜。層間絕緣採用1.0mm的環氧玻璃布板。
2)開口槽成型繞組 與半開口槽相比,cosφ較低,但嵌線方便。當採用磁性槽契后cosφ也會在很大程度上得到彌補。主絕緣、層間絕緣與1)同。
(4) 高低壓轉子成型繞組對地絕緣 成型繞組轉子的絕緣規範按轉子電壓選成型繞組的線圈通常由裸銅排按波繞組繞制裸銅排先半疊包1層0.05mm亞胺膜(6050),然後再按表3-6包槽部、端部。
為保護三合一雲母帶,端部的外層再包1層0.1×20mm的玻璃絲帶。
轉子繞組絕緣規範
轉子電壓 /V 槽部卷包0.17mm
有機硅雲母箔(G844—1) 端部半疊包0.14mm×25mm三合一雲母帶(G446—1)<600 3层 2层600~1000 4层 3层>1000 5層 4層若轉子鐵芯的質量不十分理想,槽內不太整齊,嵌線時,槽內 加1層0.2~0.25mm的NMN作為補強的槽絕緣。因此,當加補強的槽絕緣后,轉子電壓<600V時,主絕緣的單邊厚度≈0.8mm;轉子電壓=600~1000V時,主絕緣的單邊厚度≈0.95mm;轉子電壓>1000V時,主絕緣的單邊厚度≈1.1mm.
(5).高壓定子成型繞組對地絕緣 目前國內高壓電機定子成型繞組的絕緣工藝有“VPI”、“熱模壓”兩種。
1)VPI工藝
VPI的含義是真空、加壓、整體浸漬的英文縮寫。自20世紀70年代末引入國內已有30年的應用史。因其絕緣強度、機械強度及耐潮、耐腐蝕性能均好,導熱性好,又有助于降低電機溫升,故被廣氾地用於高壓電機及中型低壓電機定、轉子繞組的浸漬工藝上。但在包紮層數及單邊絕緣厚度的控制上,彼此相差不大。以採用0.14mm×25mm的5438—1環氧粉雲母帶為例:
3KV,半疊包6~8層,單邊絕緣層厚度約1.3~1.5mm;
6KV,半疊包9~11層,單邊絕緣層厚度約1.8~2.0mm
10KV,半疊包12~14層,單邊絕緣層厚度約2.8~3.0mm
嵌線時,原我公司習慣加1層0.1mm的NMN作為槽絕緣(此時主絕緣雲母帶的包紮層數也因此而適當地減少);同時也習慣在嵌線時用0.1mm的聚酯薄膜作“替紙”,線圈嵌入槽中后再抽出來,給下一個槽用。
但 區別還在選用的雲母帶的含膠量,以及由此而導致的單邊主絕緣層的厚度上。有的廠家採用5449雲母帶(含膠量為28%~32%)或5444雲母帶(含膠量為17%~23%),或5438-1雲母帶,它們都屬於“中膠帶”其3KV、6KV、10KV時包紮層數及單邊絕緣層厚度如上述。
目前我公司多數情況採用5442-1或5446雲母帶(含膠量為5%~11%),它們被稱為“少膠帶”。採用少膠帶時,包紮的雲母帶層數可以減少,大約是中膠帶的75%。因此,單邊絕緣層厚度也就減薄了,但是絕緣強度並沒減弱,應該說少膠帶VPI是發展方向。
質量及售后服務承諾:我公司產品嚴格按照國家標準,經嚴格檢驗后出廠,若貴單位在正確安裝、使用過程中發現產品有任何質量問題,我公司將在12小時內作出明確回復,如有必要,于24小時內派出工程技術人員前往現場處理問題,及時排除故障,保証產品正常使用。
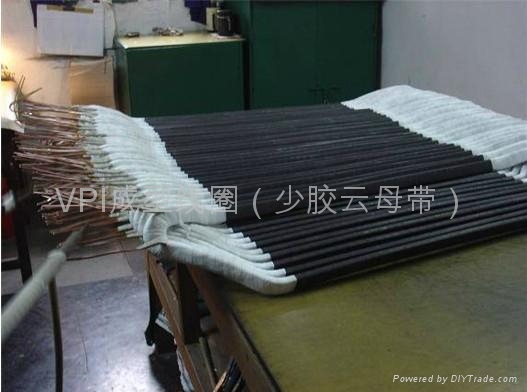